Titanium is one of the most abundant metals in the world and is known for its high corrosion resistance, strength and light weight. Although it is the fourth most common metal in the earth’s crust after aluminium, iron and magnesium, titanium is still not common because of the difficulties in extracting and mining it. However, given its versatile properties, titanium is suitable in many car applications and is already used in the aviation and aerospace industries.
Rising costs of fuel and fuel-efficient aircraft
The cost of purchasing an aircraft is already high, even before hiring personnel such as pilots and flying crew. Fuel costs also represent a huge chunk of an airline’s profits, making it logical to buy an aeroplane that is lightweight and a fuel-saver.
Titanium has been replacing aluminum parts in the production of commercial and military aircraft because of its high resistance to heat and corrosion. Furthermore, lighter airplanes also consume less fuel. Hence, titanium is now used in several parts of an aircraft such as frames, fastening elements, and landing gear. Aircraft manufacturers are also beginning to use titanium in making engine parts due to the ability of the element to withstand extreme ranges of temperatures from subzero digits to 600°C. Thus, titanium is used in discs, shafts, casings and blades of engines, and this practice has primed engineers for its use in the auto industry.
Replicating titanium applications on cars
In automobile manufacturing, titanium is also making an impact, driven by the need to look for alternative sources of materials in production apart from the traditional steel and aluminium. Several titanium grades are available that may be suitable for specific applications in the car industry. It is already used in making engines, where titanium alloy connecting rods improve fuel consumption and reduce emissions. Automotive engine valves made of the same material also improve fuel efficiency and enhance vehicle reliability. Compared to steel valve, the speed limit of engines fitted with titanium is increased by 20%.
Other car applications where titanium is used include valve spring seats, titanium spring and turbochargers. Ideally, valve spring seats must be strong and robust. This can be obtained using beta titanium alloy heat treatment. For example, Mitsubishi Motors employs titanium alloy valve spring seats, reducing the mass by 43% in comparison to using a steel lock. Moreover, the valve mechanism also increases the maximum engine speed to 300r/minute, according to Refractory Metals.
Extending the life of car parts
Another reason why titanium is used in cars is that it can extend the life of automobile parts. For example, titanium springs are better at resisting corrosion compared with steel springs, which prolong their service life.
Turbochargers benefit as well from titanium, improving heat resistance and durability. Light metals such as aluminium are not desirable in turbochargers, which boost the power output of an engine, because of their low melting point. However, titanium with its high resistance to heat, makes a good material for turbochargers, improving their service life. Mitsubishi has already replicated the technology in its Lancer Evolution model of vehicles.
Other car parts that also benefit from using titanium are the titanium rods used in the exhaust systems of vehicles. Titanium and its alloys improve the life and reliability of exhaust systems, as well as enhance fuel burn efficiency. Upscale brand, Porsche, talks of using hand-made titanium exhaust for its 935 model, one of the greatest race cars in history. Porsche will make 77 units of the model, and the car is intended for track use only.
Titanium in the car frame
In addition to auto parts, titanium is also viewed as a suitable material for the body frames of cars because of its high strength, anti-corrosion properties, hardness and high heat resistance. Its light weight improves car performance considerably.
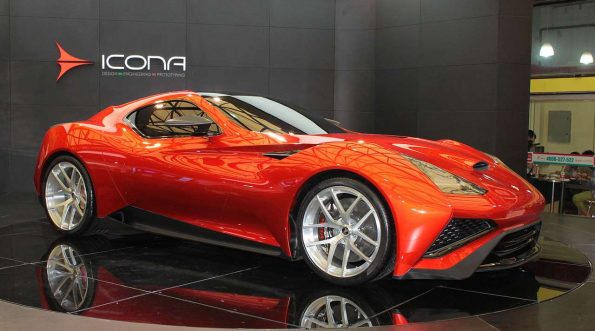
To illustrate, Icona, an Italian design house, created a hypercar made of a titanium and carbon fibre body. The Vulcano Titanium is a luxury vehicle with a maximum torque of 819 Nm and a top speed of over 350km/h. It carries a hefty price tag of US$2.78 million.
Restrictions of titanium in automobile applications
Unfortunately, the main strengths of titanium can work against it. It is an expensive and problematic material to work with, which drives the price up. It may also be more difficult to repair, and won’t crumple in a collision due to its hardness. Critics argue that, because of its lack of elasticity, collisions involving cars made of titanium can increase the risk of injuries or death. In the case of the Vulcano, combining titanium with carbon fibre counteracts the rigidity of titanium.
Titanium has many desirable properties and characteristics that are suitable for car production. Finding low-cost titanium alloys for use in mass automobile production is key to enhancing its adoption and improving car performance, safety and reliability.